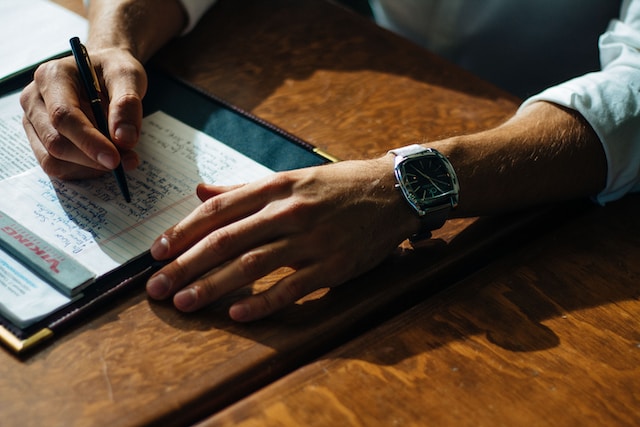
Trabalhar Como Jornalista de Notícias Sobre Jogos de Azar: Vantagens e Desvantagens
A oportunidade de trabalhar em projetos desafiadores e causar impacto é uma das muitas razões pelas quais Paolo, que é …
Escola de Jornalismo
Escola de Jornalismo
Jornalista é uma profissão interessante para pessoas sociáveis e curiosas. Pressupõe contato constante com pessoas e participação em eventos. Muitos de seus representantes se tornam pessoas famosas e líderes de opinião. No artigo você descobrirá o que os jornalistas estão fazendo e onde são solicitados, obtenha uma descrição detalhada desse trabalho.
A essência da profissão de jornalista é a busca e o processamento de informações interessantes e importantes para a sociedade. Com base nos dados coletados, são publicados notícias, artigos, relatórios, sites de rádio, televisão e Internet.
Em seus materiais, os jornalistas podem chamar a atenção para os problemas, provocar discussões públicas, refletir diferentes pontos de vista sobre quaisquer eventos. Existem especialistas do setor que cobrem eventos em uma área específica, por exemplo: economia, finanças, educação, entre outros.
No processo de trabalho, os jornalistas se comunicam muito, fazem viagens de negócios, inclusive ao exterior. Entrevistas, fotografias e outras …
Saber maisO nível de rendimento depende do ramo de atividade, profissionalismo, experiência, marca pessoal. Por exemplo, os altos salários são tradicionalmente …
Saber maisCom o desenvolvimento dos blogs, a mídia tradicional está sob pressão. Existe a opinião de que a demanda pela profissão …
Saber maisO mais importante no jornalismo é a capacidade de encontrar informações valiosas para os leitores e transmiti-las rapidamente ao público. …
Saber maisJornalista é uma profissão interessante para pessoas sociáveis e curiosas. Pressupõe contato constante com pessoas e participação em eventos. Muitos de seus representantes se tornam pessoas famosas e líderes de opinião. No artigo você descobrirá o que os jornalistas estão fazendo e onde são solicitados, obtenha uma descrição detalhada desse trabalho.
No bloco sobre jornalismo, você aprenderá a criar textos de notícias; analisaremos com você quais fontes de informação existem, quais informações podem ser confiáveis e quais fatos precisam ser verificados novamente. Reportagem, entrevista, ensaio – esses conceitos serão preenchidos com significados, você aprenderá a criar textos jornalísticos em diferentes gêneros. Falaremos sobre como funciona a economia da mídia, por quanto tempo viverá a imprensa escrita e qual é o futuro da televisão e do rádio. Você vai mergulhar no mundo das histórias que refletem e criam a realidade que nos rodeia.
A oportunidade de trabalhar em projetos desafiadores e causar impacto é uma das muitas razões pelas quais Paolo, que é …
Podemos ajudá-lo a encontrar o que procura?